5 Things to Consider When Moving Your Manufacturing Warehouse
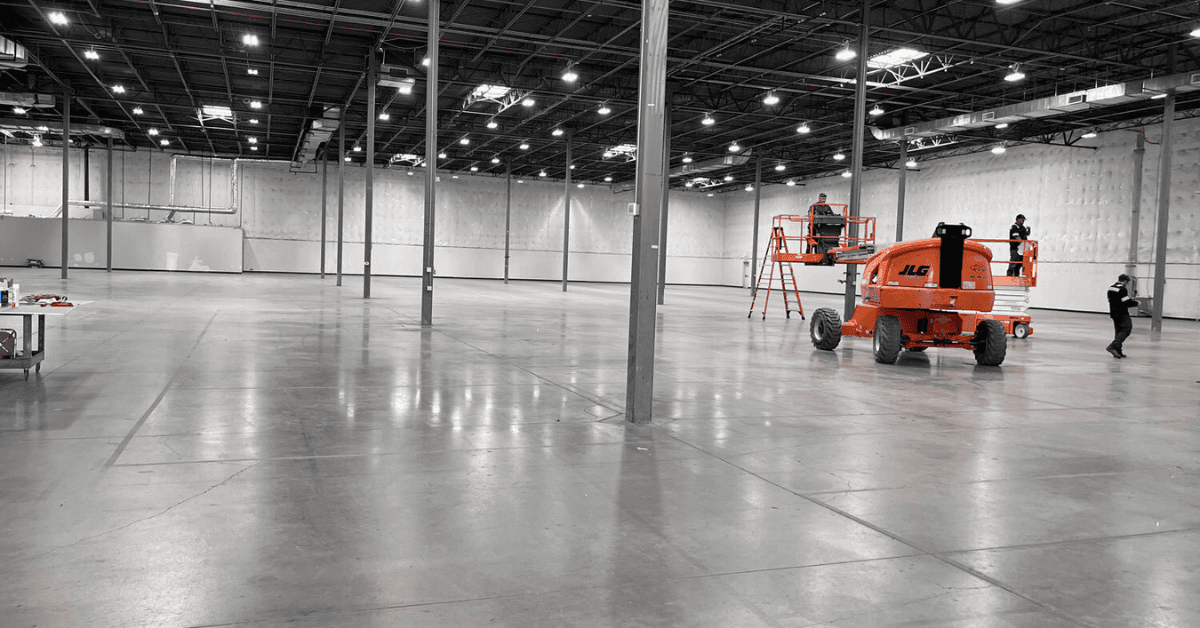
Manufacturers face unique needs when addressing warehousing variables that impact their business and supply chain. They may be growing, downsizing or decommissioning their off-site warehousing space. They may be consolidating warehouses or moving to more central locations. They may be switching to an outsourced model or adding storage for seasonal goods. Whatever the reason, warehouse relocations are regular occurrences for the manufacturing industry.
Atlanta’s manufacturing presence is continuing to grow, according to the Atlanta Business Chronicle. As manufacturing companies expand in the Atlanta metro, more leaders are rethinking the sizes, layouts and workflows of their current warehouses. If you are relocating your warehouse across the city or joining the Atlanta metro for the first time, here are five things to consider when planning your manufacturing move.
1. Layout
The locations of your warehouses play vital roles in the efficiency of your supply chain. Before you sign the lease for a new warehouse, make sure it’s located in a central area that will simplify your transportation needs. Then, consider the layout of your existing and future warehouse. In an efficient manufacturing warehouse, every aisle, cell or station is designed to streamline your everyday operations. If your current warehouse is not operating as smoothly as you need it to, now is the time to rethink your setup. Work with your relocation partner to develop Computer-Aided Design (CAD) drawings that show exactly where everything will go in your new warehouse. Together, you can tweak, test and refine the layout before you ever begin moving boxes.
2. Regulations
Minimizing downtime is key to any manufacturing move. Avoid last-minute snags in your warehouse relocation by checking the regulatory and permitting requirements for your area as early as possible. In Atlanta, the city’s Fire Plan Review for rack storage requires information on your commodities, packing and storage procedures, scaled floor plans and aisle widths, the warehouse’s maximum storage height and more. Before you can begin placing inventory on the new racks, you must complete this permitting process and receive approval from the city. City officials may also require additional signage or emergency lighting after they’ve walked through your space. An experienced moving partner will know how to efficiently navigate the complexities of your relocation process. Your dedicated move coordinator will help keep your move on track, keeping you informed every step of the way.
3. Timeline
For other kinds of relocations, you may be able to move all of your assets over at once without facing significant disruptions. However, manufacturing moves cannot occur in a single day, and attempting to do so would interrupt your supply chain and negatively affect your bottom line. Work with your relocation partner to create an extended moving schedule that builds in time for unforeseen delays. Start by only moving a few racks over to your new warehouse. While your relocation partner installs and organizes them, you can continue normal operations in your current space. By creating an overlapping schedule, you give your company time to resolve issues in your new space before completely decommissioning the original one.
4. Inventory
Do a full inventory of your warehouse and consider getting rid of any obsolete stock that’s been collecting dust. Your relocation partner can help you dispose of any unwanted materials in a cost-effective, environmentally conscious manner. Your partner can also provide storage and supply-chain support if you need to purchase new racks for the relocation, as well as securely pack, install and uninstall your assets and equipment according to the industry’s best practices. Make sure that your moving company has tracking capabilities so you can keep an eye on your assets at every step of the relocation process.
5. Future
Before you move, make sure you’ve taken future growth into consideration. Does your new warehouse offer provide the opportunity to continue scaling operations over time? Insufficient space can impede your growth by cluttering your process for receiving, organizing, storing and fulfilling orders. If you need to prepare your company to scale without the overhead investment, consider partnering with a third-party logistics company (3PL) instead of opening a new warehouse. A 3PL allows you to tap into its asset network, giving you the freedom to expand your business without the need to invest in your own warehouses and transportation.
An experienced relocation partner can transform your company’s moving experience. Armstrong – Atlanta offers dedicated support to drive efficiency in your manufacturing business and every inch of your warehouse. Start planning your warehousing move today by calling our experts at 770.368.0368 or requesting a free quote online.