Essential Guide to Charlotte Construction Material Storage in a Rapidly Growing City
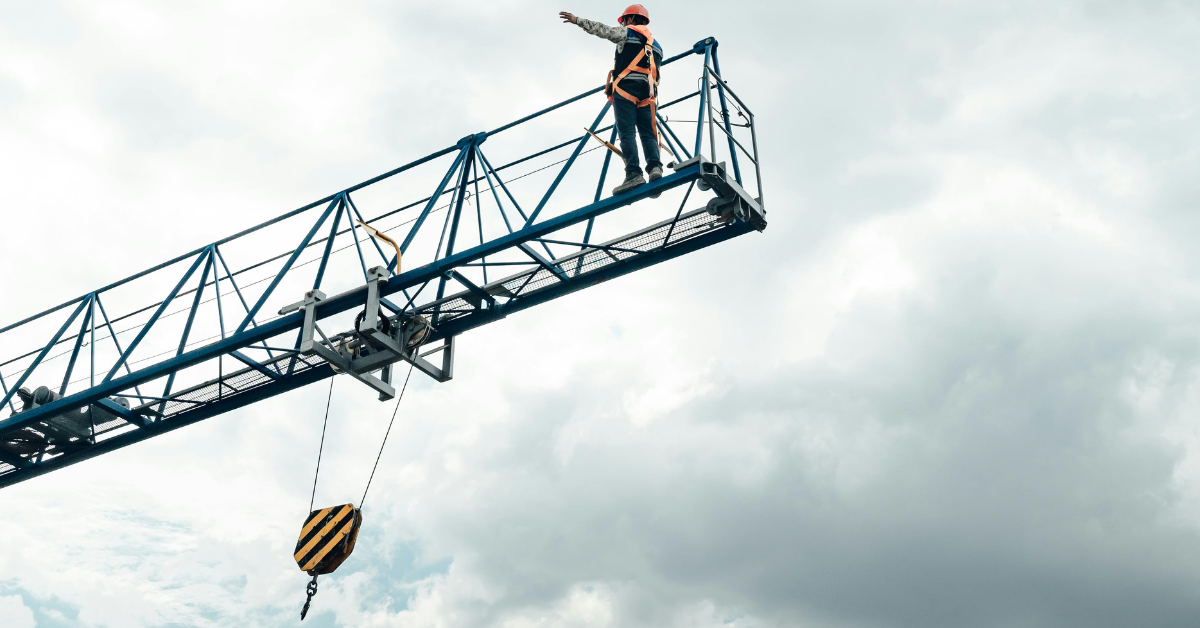
Charlotte, NC is one of the nation’s fastest-growing cities, spurred by economic opportunity and a high quality of life. This expansion has fueled a construction boom, bringing new challenges for material storage. As construction companies race to meet demand, efficient material storage solutions have become essential. The following guide explores the impact of Charlotte’s growth on the construction industry and highlights best practices for storing materials effectively in the region.
Key Factors Driving Charlotte’s Growth
Charlotte’s rapid expansion is fueled by diverse strategic factors, making it one of the most attractive cities for development and construction. Here’s a closer look at the main drivers shaping Charlotte’s growth trajectory:
1. High Quality of Life and Economic Opportunities
Charlotte’s dynamic lifestyle, top-rated educational institutions and diverse employment opportunities draw new residents and businesses alike. The city’s appeal is heightened by its affordability compared to other large metropolitan areas, offering a balance of urban amenities and a welcoming community atmosphere.
2. Business-Friendly Environment
Charlotte’s favorable tax policies, streamlined regulatory landscape and attractive business incentives have made it a prime destination for corporate and office relocations. These factors attract large corporations and support small to mid-sized businesses, fueling economic growth across diverse sectors.
Charlotte’s proactive approach to fostering a supportive business ecosystem has encouraged numerous companies to establish headquarters or expand operations here, stimulating demand for new office buildings, warehouses and facilities. For businesses considering office relocation, Charlotte’s well-connected infrastructure, skilled workforce and vibrant local economy provide an ideal environment for growth.
3. Revitalized Manufacturing Sector
Charlotte’s origins as a textile manufacturing hub paved the way for its transformation into a dynamic center for manufacturing and logistics. Today, manufacturing remains a vital contributor to the city’s economy, now encompassing advanced manufacturing, automotive and aerospace sectors. This diversification has strengthened economic stability and fueled demand for industrial spaces, warehouses and logistics facilities.
The rise of first and final-mile logistics has further impacted warehousing in Charlotte. As international suppliers strive to meet the increasing demands of U.S. manufacturers, these logistics processes play a critical role in reducing delivery times and ensuring inventory availability. Charlotte’s strategic location and robust transportation network make it an ideal hub for managing first-mile shipments from overseas manufacturers and final-mile deliveries to local facilities, enabling a seamless, end-to-end supply chain.
4. Accessibility and Infrastructure Growth
Infrastructure advancements are key to Charlotte’s growth, especially with transit expansions and improved connectivity across South Charlotte, North End and the Applied Innovation Corridor. These developments include new light rail extensions, upgraded road networks and the expansion of Charlotte Douglas International Airport.
For the construction industry, this infrastructure growth has opened up new zones for commercial and residential construction projects, making it easier to move materials, equipment and personnel throughout the city.
Storage Challenges in Charlotte’s Construction Industry
Charlotte’s rapid growth presents unique challenges for the construction industry, especially regarding material storage.
- Demand for Storage Space: With construction sites dispersed across York County and Mecklenburg County and in particular, South End, the need for decentralized storage solutions has grown. Companies must consider the space required for storage and the logistics of transporting materials between various locations.
- Specific Storage Requirements: Construction materials range widely, from raw resources like lumber and steel to finished goods like tiles and fittings. Each material type requires specific storage conditions to prevent damage and ensure safety.
The Role of Effective Supply Chain Management
Effective Construction Supply Chain Management is crucial for overcoming storage and transportation challenges in Charlotte’s expanding construction landscape. This approach involves coordinating the flow of materials and equipment to ensure timely delivery to multiple construction sites, optimizing logistics and reducing the need for extensive on-site storage. By synchronizing supplier and contractor schedules, supply chain management helps minimize delays, reduces storage costs and ensures that resources are available exactly when needed. In a fast-paced environment like Charlotte’s, efficient supply chain management is essential to maintaining project timelines and meeting the demands of a growing industry.
Storing Construction Materials
Selecting appropriate storage solutions is essential, particularly in a city with Charlotte’s climate variability and high demand for space. Proper storage preserves the quality of materials and supports efficient project timelines by ensuring materials are readily accessible and in good condition.
1. Choosing the Right Storage Space
Climate control, security and environmental conditions are key to maintaining material quality, particularly in Charlotte’s humid summer months. Construction companies have several storage options, including on-site storage, a rented storage unit and mobile storage solutions. Companies can minimize damage and reduce transport delays by choosing storage solutions that align with material requirements and logistics.
2. Protecting Specific Materials
Certain materials require special handling and storage conditions to prevent degradation. Here are tips for storing critical building materials:
- Lumber: Store lumber horizontally and cover it to prevent warping from moisture exposure. Elevated storage, away from direct contact with the ground, helps avoid moisture buildup.
- Bricks: Keep bricks off the ground to prevent moisture absorption and use a waterproof tarp to shield them from rain. Elevating bricks and covering them properly reduces the risk of water damage and ensures they are in optimal condition for use.
- Tiles: Store tiles in a cool, dry place to prevent cracking and discoloration. Stacking them securely and protecting them from temperature extremes extends their lifespan and keeps them ready for installation.
3. Safety and Security
As Charlotte’s construction industry grows, the importance of robust safety and security measures in material storage also increases.
- Preventing Theft and Vandalism: Safeguarding materials and equipment is essential. Standard practices such as surveillance, GPS tracking and secure fencing help reduce the risk of theft at construction sites.
- Maintaining a Safe Storage Environment: Proper lighting, clear signage and established safety protocols create a secure workspace for employees. Hazardous materials should be clearly labeled, and staff should be trained in safe handling practices.
Heavy Equipment Storage for Construction Machinery
Charlotte’s development goes by hand with construction machinery. Storing heavy construction equipment requires specialized facilities and practices to ensure machinery remains secure, in good condition and readily accessible. With large investments in equipment such as excavators, bulldozers, cranes and loaders, construction companies must adopt effective storage solutions to protect these assets and support operational efficiency.
- Weatherproofing and Protection: Due to its size, heavy equipment often requires outdoor storage, making weather protection essential. Heavy-duty tarps, covers, or shrink-wrap protect against rain, dust and sun exposure, which can lead to corrosion and fading. In Charlotte’s variable climate, weather-resistant coatings and anti-corrosion sprays are advisable for added protection during extended storage.
- Routine Maintenance and Inspections: Regular inspections and maintenance extend machinery life and minimize downtime. Storage spaces should accommodate checks on fluids, batteries and general cleanliness. Monthly operational tests on hydraulic equipment keep components lubricated and ready for use.
- Positioning and Weight Distribution: Equipment should be stored on stable, level surfaces to prevent imbalance or stress, which can lead to mechanical wear or tire damage. Lowering hydraulics and securing wheels help maintain stability, especially for long-term storage.
The Importance of Inventory Management System
Effective inventory management is essential for meeting Charlotte’s growing construction demands. A thorough understanding of the types of materials used and their specific storage requirements helps prevent loss, reduce waste and keep projects running smoothly and on schedule. Implementing a robust inventory management system can streamline material tracking, ensure accountability and provide real-time insights, enhancing overall project efficiency.
With construction sites often spread across multiple locations, a well-organized inventory system enables teams to track materials efficiently, minimizing delays and costly reorders. Construction companies often face the challenge of managing decentralized sites, making real-time material tracking difficult. Given the vast array of items required for different projects, accurate tracking and accountability are crucial for maintaining project continuity and preventing resource shortages.
Best Practices for Construction Inventory Management
Efficient material storage in construction goes beyond logistics; it requires a safe, well-organized and environmentally responsible approach to maximize productivity and minimize costs. Adopting the following practices helps construction companies manage resources effectively, control inventory and reduce environmental impact.
- Training and Regular Inspections: Ongoing training ensures that employees are familiar with safety protocols, proper material handling and storage techniques, reducing the risk of accidents and material mishandling. Regular inspections help identify potential hazards, verify storage compliance with safety standards and maintain an organized, secure environment.
- Environmentally Friendly Disposal: Proper disposal of construction materials supports regulatory compliance and minimizes waste. Adopting eco-friendly practices—such as recycling or repurposing materials—reduces landfill use and contributes to a more sustainable construction process. Following local guidelines ensures a positive environmental impact and prevents potential fines.
- Implementing Digital Inventory Management Solutions: Digital tools are invaluable for efficient and safe inventory management. Advanced inventory software can provide real-time stock updates, track high-value equipment and minimize delays, improving overall productivity and controlling costs. Integrated systems enable seamless planning, tracking and reporting, allowing teams to optimize inventory management and streamline project workflows.
- Maintaining Organized, Secure Storage Facilities: Well-organized storage facilities minimize errors, prevent damage and allow for quicker access to materials, supporting project timelines and maintaining resource availability.
By implementing these best practices, construction companies can manage inventory efficiently, maintain project continuity and ensure safe, sustainable and effective material storage in Charlotte’s competitive construction landscape.
Organizing and Labeling Construction Materials
Proper organization ensures safety, reduces losses and facilitates efficient project timelines. Keeping similar items together prevents accidents and simplifies access, especially for larger projects that require multiple types of materials.
Color-coding systems and digital labels make locating materials faster, especially when dealing with large quantities of various types. This method also aids in inventory management, ensuring accurate tracking and reducing the risk of misplacement.
Maximizing Efficiency and Safety: Key Takeaways for Charlotte’s Growing Construction Industry
Companies must prioritize efficient storage and inventory management to thrive in Charlotte’s bustling construction landscape. Properly storing materials, using effective tracking systems and training staff on handling procedures can help prevent accidents, reduce waste and keep projects on schedule. By adopting these strategies, your construction company can meet the city’s growing demand while ensuring safety and operational efficiency.
Are you considering relocating your business to Charlotte? Explore Armstrong’s packing and moving services, and let our local Charlotte movers handle the logistics so you can stay focused on your business.