Tips for Relocating to a New Warehouse in Atlanta
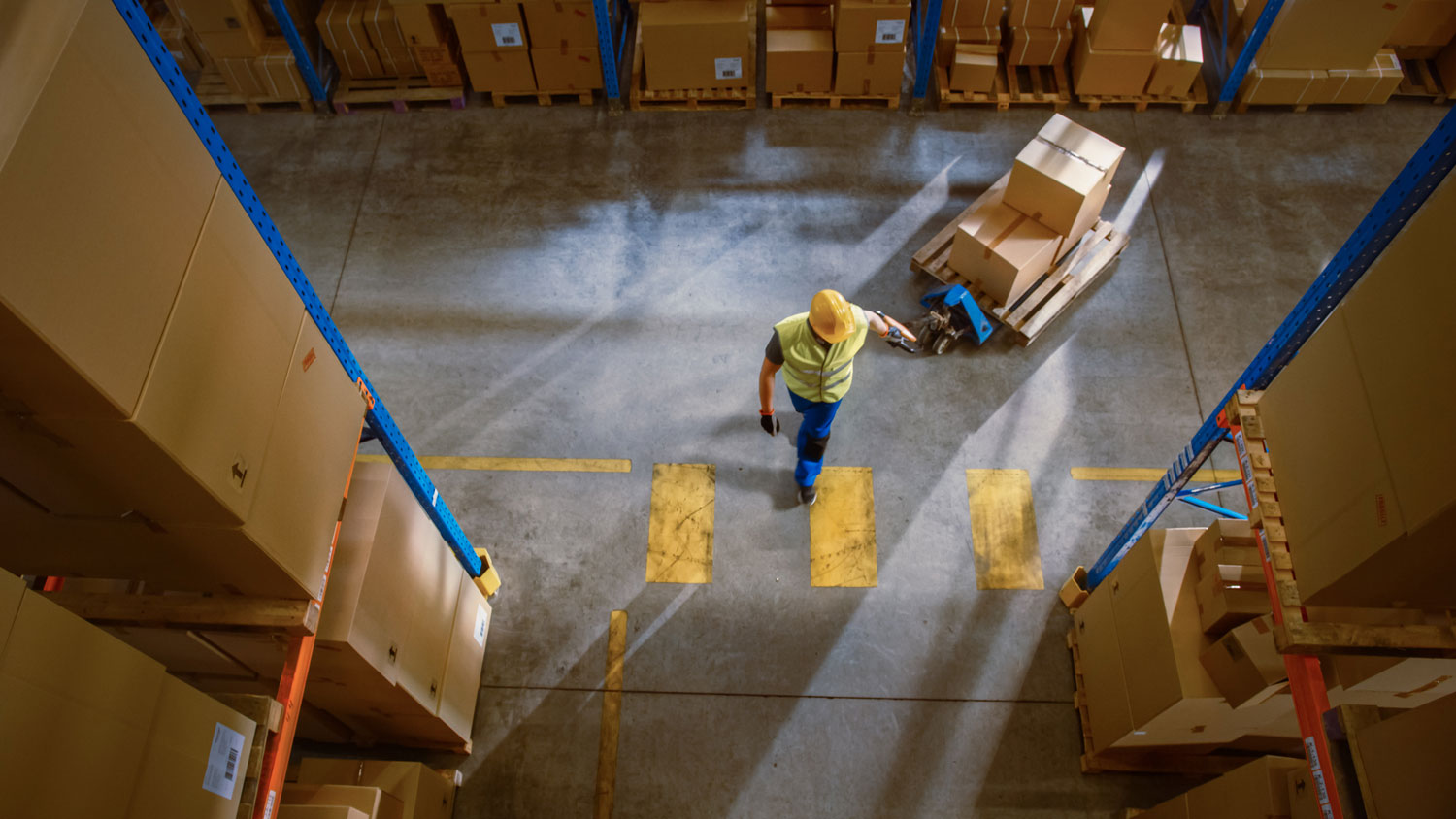
Amid global supply-chain disruptions, the warehousing market is growing fast, dropping national vacancy rates to an all-time low.
The increased demand for industrial space is pushing companies across the country to relocate to larger facilities to accommodate new trends. However, relocating a warehouse can seem needlessly complex, requiring months to years of careful planning.
Thinking about joining the hordes of warehouses relocating to and within the Atlanta market? Here are five tips to ensure your move is smooth and your downtime is minimal.
Know the local regulations and exemptions.
Start by familiarizing yourself with the Department of City Planning’s rack storage permitting requirements. Before placing anything on racks in the new warehouse, you’ll have to complete commodity affidavit and racking permit forms, provide floor plans of the new facility and complete an inventory sheet for any hazardous materials. Prevent wasted hours and unnecessary headaches down the line by considering these regulations now.
If you’re relocating to Georgia from a different state, make sure you understand the regional tax structure. Moving a manufacturing warehouse may result in tax exemptions on machinery, packaging, raw materials and more purchases. Additionally, many Georgia counties won’t charge property tax on distribution centers that have $5 million or more invested and plans to ship inventory within the year.
Find a location that minimizes transit time.
Maximize efficiency and cost savings by choosing a strategic warehousing location that allows convenient access to local ports. Georgia is home to two deep-water ports and three inland terminals, which are valuable hubs for global trade. The past few years have been record-breaking for the Georgia Ports Authority, exploding its annual terminal capacity, tonnage volume and gate moves.
The Atlanta metro is a little over an hour’s drive from inland ports in Columbus and Chatsworth. However, The American Transportation Research Institute found that the Atlanta metro has some of the worst traffic bottlenecks in the country, with three local spots landing in the top 20. Keeping local transit time to a minimum will ensure your processes and personnel stay productive.
Design for efficient warehouse product flow.
Relocating to a new facility is the perfect opportunity to analyze product flow and create a layout that makes the most of your space. If you have a Warehouse Management System, dive into the collected operational data to determine the speed, flow and frequency with which products move through the facility.
Then, make sure your new warehouse has the correct number of bays and determine the most effective ways to layout the facility. A U-shaped design is arguably the most common because of its ability to reduce product handling, but L-shaped and I-shaped structures can provide additional security for high-volume warehouses.
Check your layout against safety requirements.
Consider how much space your warehousing equipment will need to move smoothly and safely throughout the area. The Occupational Safety and Health Administration (OSHA) recommends making the aisles at least three feet wider than your bulkiest piece of equipment. Most forklifts need 12 feet or more to operate efficiently.
OSHA also emphasizes the importance of designing your facility in a way that requires personnel to twist, reach and bend as little as possible to prevent injuries. Other factors such as clear aisle markings and quality lighting can ensure high visibility, safety and productivity in your warehouse.
Aim for 85-percent space utilization.
On average, you should aim to use 85-88 percent of your storage space in any given month. This commonly touted sweet spot allows companies to avoid having wasted space or empty racks. Work your way backward to determine the size, spacing and racking you need to achieve your ideal utilization rate.
These five tips barely scratch the surface of the meticulous planning, coordination and expertise required for warehouse relocations. Consider partnering with a third-party logistics provider (3PL) to ensure you don’t miss a single step and are set up for success in your new space.
The Armstrong Company provides relocation and logistics services to ensure your operations stay efficient before, during and after your warehousing move. Our award-winning crews and array of services reduce risk, downtime and liability for companies nationwide. Get started today by calling the Armstrong – Atlanta team at 770.368.0368 or requesting a free quote online.